来源:http://blog.sina.com.cn/s/blog_ace9fcbc0102ymx0.html
预测性维护{维修}(Predictive Maintenance,简称PdM)(又称:预知性、预见性维护{维修})是以状态为依据(Condition Based)的维护,在机器运行时,对它的主要(或需要)部位进行定期(或连续)的状态监测和故障诊断,判定装备所处的状态,预测装备状态未来的发展趋势,依据装备的状态发展趋势和可能的故障模式,预先制定预测性维护计划,确定机器应该修理的时间、内容、方式和必需的技术和物资支持。预测性维护集装备状态监测、故障诊断、故障(状态)预测、维护决策支持和维护活动于一体,是一种新兴的维护方式。
预测性维护不仅在名字称呼上有不同,在概念的内涵和外延上也有出入,因此又有狭义和广义预测性维护两种概念。
狭义的预测性维护立足于“状态监测”,强调的是“故障诊断”,是指不定期或连续地对设备进行状态监测,根据其结果,查明装备有无状态异常或故障趋势,再适时地安排维护。狭义的预测性维护不固定维护周期,仅仅通过监测和诊断到的结果来适时地安排维护计划,它强调的是监测、诊断和维护三位一体的过程,这种思想广泛适用于流程工业和大规模生产方式。
广义的预测性维护将状态监测、故障诊断、状态预测和维护决策多位合一体,状态监测和故障诊断是基础,状态预测是重点,维护决策得出最终的维护活动要求。广义的预测性维护是一个系统的过程,它将维护管理纳入了预测性维护的范畴,通盘考虑整个维护过程,直至得出与维护活动相关的内容。
修复性维护(Corrective Maintenance),又称事后维护(Break-down Maintenance),是“有故障才维护(Failure Based)”的方式,它是以设备是否完好或是否能用为依据的维护,只在设备部分或全部故障后再恢复其原始状态,也就是用坏后再修理,属于非计划性维护。
预防性维护(Preventive Maintenance)又称定时维护,是以时间为依据(Time Based)的维护,它根据生产计划和经验,按规定的时间间隔进行停机检查、解体、更换零部件,以预防损坏、继发性毁坏及生产损失。这种维护方法也就是目前所普遍采用的计划维护或定期维护,如大、中、小修等。
预测性维护的相关概念
预测性维护最早在西方发达工业国家兴起,预测性维护的概念源起于英文名词“Predictive Maintenance”,到现在为止,预测性维护已经有了几个相似的名字,这是因为在不同领域,不同的人员根据自己研究的侧重点不同,给出了不同的翻译和不同的定义。追根溯源,应该从英文的定义谈起。
Predictive Maintenance,其英文解释为Condition Based Maintenance(CBM)或On-condition Maintenance。PdM一般翻译为预测性维护或预知性维护,而预测维护和预知维护与前面的翻译相比,仅仅是多字少字的问题;CBM一般翻译为状态基维护或基于状态的维护,这个翻译按英文字面的意思直译过来,同时引入了“基”的概念,使翻译专业化。有时CBM也被翻译为预测性维护,因为它的英文原意就是对PdM的概念解释;On-condition Maintenance一般翻译为视情维护,这是翻译者根据中国人的习惯意译过来的。在实际运用中,几个中英文名词有时被随机地组合,这都无可厚非,因为它们本身是一回事。
沿袭运用到今天,几个名词在概念上有了一些细微的差别。预知性维护被定义为:以设备诊断技术为基础,结合设备故障的历史和现状,参考运行环境及其它同类设备的运行情况,应用系统工程的方法进行综合判断分析,从而查明设备内部情况、故障和异常的性质,预测隐患的发展趋势,提出防范措施和治理对策,这样一套方法总称为预测方法,把应用预测方法得到的结果纳入维护管理就是预知维护。它强调了预测方法,包罗了维护管理;而基于状态的维护和视情维护立足于状态,强调了状态,它们的理论依据是:机械和装备有自己的状态,即将出现问题的机械或装备将出现一些可以观察、感觉或测量到的信号(如噪声、振动、发热、裂纹或电量的改变等)。这里状态有两层含义,一是指在某时某刻某种条件下装备的即时状态,这是狭义的状态的概念。二是包含了即时状态的前身和后续,指的是整个生命周期内的状态,即广义的状态概念。
《中国制造2025》提出“加快开展物联网技术研发和应用示范,培育智能监测、远程诊断管理、全产业链追溯等工业互联网新应用。实施工业云及工业大数据创新应用试点,建设一批高质量的工业云服务和工业大数据平台”。2025计划中提到的智能监测、远程诊断与工业云和工业大数据平台的深度融合指明了智能(预知性预测性预见性)维护领域的最新发展方向。
智能维护属于预测性(预知性)维护,是对设备和产品性能衰退过程的速测和评估, 旨在保障企业产品加工制造系统的“零故障”。在工业智能制造领域,智能维护网提出“工业智能维护”的概念,主要是利用物联网技术和装备监控技术与无线传感技术使企业管理技术和信息技术全面融合,实现管理过程自动化、数字化、智能化、智慧化的全过程,并加上绿色智能的手段和智慧系统等新兴技术于一体,协助企业打造高效节能的、绿色环保的、环境舒适的智能化工厂。
预测性维护技术体系
预测性维护发展到现在,基本上形成了自己的技术体系,如图所示。
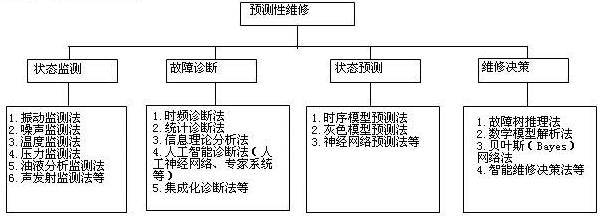
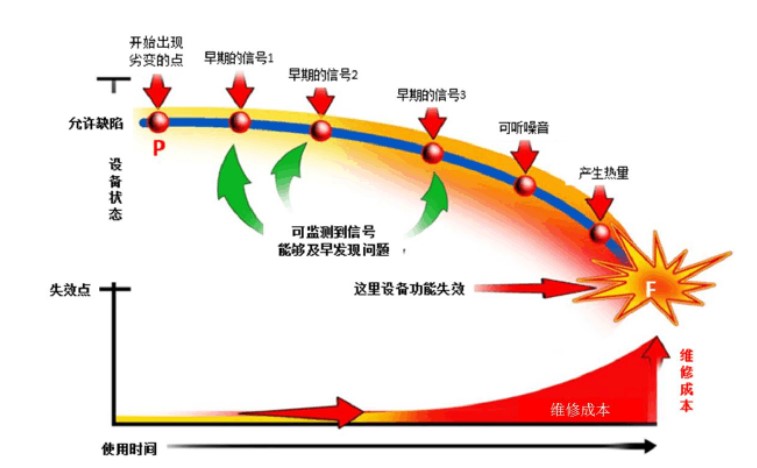
1.状态监测技术
状态监测技术发展到现在,在各工程领域都形成了各自的监测方法,状态监测的方法依据状态检测手段的不同而分成许多种,常用的包括:振动监测法、噪声监测法、温度监测法、压力监测法、油液分析监测法、声发射监测法等。
2.故障诊断技术
单讲“故障诊断”,它是一门新发展的科学,而且越来越受到重视,尤其是在连续生产系统中,故障诊断有着非常重要的意义。按照诊断的方法原理,故障诊断可分为:时频诊断法、统计诊断法、信息理论分析法及其它人工智能法(专家系统诊断、人工神经网络诊断等)、模糊诊断、灰色系统理论诊断及集成化诊断(如模糊专家系统故障诊断、神经网络专家系统故障诊断、模糊神经网络诊断等)。故障诊断是指故障发生了,确实影响到设备的安全、性能、可用性之后,判断故障的原因什么。故障是一种表现,而触发这种故障的原因可能有多种。需要故障诊断工程师配合经验、数据、现场勘查才能判断故障原因。
3.状态预测技术
状态预测就是根据装备的运行信息,评估部件当前状态并预计未来的状态。其常用的方法有时序模型预测法、灰色模型预测法和神经网络预测法。而对于预测方法的开发一般有三种基本途径:物理模型、知识系统和统计模型。在实际应用中,可将三种途径综合在一起,形成一种结合了传统的物理模型和智能分析方法,并能够处理数字信息和符号信息的混合性故障预测技术,对于实现预测性维护更为有效。
4.维护决策支持与维护活动
维护决策是从人员、资源、时间、费用、效益等多方面、多角度出发,根据状态监测、故障诊断和状态预测的结果进行维护可行性分析,定出维护计划,确定维护保障资源,给出维护活动的时间、地点、人员和内容。维护决策的制定方法一般有故障树推理法、数学模型解析法、贝叶斯(Bayes)网络法(适用于表达和分析不确定和概率性事物)和智能维护决策法等。
预测性维护的最终目标是提高生产安全稳定性、有效制定并实施设备维护策略、降低设备维护成本、减少设备停工检修时间。
01引言
近些年,智能制造在流程工业生产中得到了示范应用,其重要性逐渐深入人心。国内外学者对于智能制造的理解和定义不尽相同。清华大学吴澄将智能制造定义为以智能技术为代表的新一代信息技术在制造全生命周期的应用中所涉及的理论、方法、技术和应用。智能制造时代,对于设备的可靠性要求会更高,对于设备维护管理的要求也会随之提高,制造企业、设备管理信息化厂商、预测性维护服务厂商都将参与到设备维护管理的整体环节中。
02 设备预测性维护
预测性维护是以状态为依据的维修,是对设备进行连续在线的状态监测及数据分析,诊断并预测设备故障的发展趋势,提前制定预测性维护计划并实施检维修的行为。总体来看,预测性维护中,状态监测和故障诊断是判断预测性维护是否合理的根本所在,而状态预测是承上启下的重点环节。根据故障诊断及状态预测得出的维修决策,形成维修活动建议,直至实施维修活动。可以说,预测性维护通盘考虑了设备状态监测、故障诊断、预测、维修决策支持等设备运行维护的全过程。
上述预测性维护与预防性维修不同,经常会有人将两者混淆。这里强调说明,后者是以时间为依据的维修,目的是定期检测设备健康状态、定期修复已发生的设备故障及损坏、预防继发性毁坏及设备停机故障。
相对于预防性维修,实行预测性维护制度有以下优点:
- ①避免“过剩维修”,防止因不必要的解体拆卸、更换零部件等;
- ②有效减少设备停机维修时间;
- ③尽早发现故障隐患,避免故障恶化;
- ④合理预估机械部件的剩余寿命,使设备在保证安全的情况下合理超期服役。
基于上述优势,可以说实施预测性维护是企业提高设备管理水平的必经之路,也是必然趋势。
1.1 预测性维护市场潜力
研究表明,针对预测性维护这个新兴市场,物联网(Internet of Things,IoT)平台商、云存储厂商以及提供动态数据分析的厂商发挥着越来越大的作用。基于云平台的IoT及大数据分析将对设备的预测性维护带来25%~30%的效率提升。IoT Analytics发布的针对全球预测性维护的报告中指出:预计2016~2022年,预测性维护的复合年均增长率为39%;根据这个增长速度,到2022年,市场规模将达到734.5亿元人民币。
预测性维护市场规模如图1所示。对于设备管理信息化厂商以及预测性维护服务厂商来说,打开市场、拓展市场越早越有利。
图1预测性维护市场规模
Fig.1 Market size of predictive maintenance
1.2 预测性维护技术体系
预测性维护的技术体系涵盖状态监测、故障诊断、状态预测、维修决策等4个方面。预测性维护技术体系如图2所示。状态监测技术是利用温度、压力、振动、超声波等不同类型传感器获取设备的多种运行状态信息。其中,温度传感器可用于汽轮机、空压机等大型机组的油温、瓦温监测;振动传感器广泛应用于判断机械设备的非平稳运动现象;超声波等高频传感器可用于判断设备机械部件内部的细微摩擦,对于微小故障的判断较为灵敏。通过以上多传感器数据之间的协同工作及功能互补,可实现更精确的状态监测。故障诊断涉及的方法包括时域信号诊断、频域信号诊断,以及以此为基础的人工神经网络、专家系统综合诊断。故障诊断可为设备的状态预测及维修决策提供指导意见。通过故障诊断及状态预测,设备管理者及检维修人员制定合理的维修措施及计划,并通过实施维修,验证设备状态监测及故障诊断的合理性及准确性。
图2 预测性维护技术体系
Fig.2 Technical system of predictive maintenance
03 设备故障诊断
在制造企业的生产环节中,生产与管理之间的关系可以描述为:系统的自由度决定了管理的复杂程度。对智能制造来说,系统的自由度越小,系统的可靠性要求越高,对于设备管理者及检维修人员的要求也会随之提高。设备管理者需要在生产系统自由度降低的情况下实现更优化、更简化、更智能化的设备状态监测诊断过程,并以高准确性、高精确性的诊断结论指导检维修实施及设备恢复生产。
图3设备故障诊断流程图
Fig.3 Flowchart of equipment fault diagnosis
现阶段预测性维护中的故障诊断主要依靠人工分析实现,诊断分析人员通过趋势、波形、频谱等专业分析工具,结合传动结构、机械部件参数等信息,实现设备故障的精准定位。笔者相信,未来的预测性维护将是建立在物联网及人工智能技术上的智能诊断,届时诊断效率和准确性都将获得大幅提升。本文将重点介绍物联网技术在设备状态监测诊断中的应用前景及实施方案。
04 物联网技术的应用
物联网技术为设备状态监测诊断带来了设备状态无线监测、高速数据传输、边缘计算和精细化诊断分析等先进技术。在设备状态监测诊断中应用物联网技术,面向企业数字化、网络化、智能化需求,构建精准、实时、高效的数据采集互联体系。其核心意义在于构建基于海量数据采集、汇聚、分析的服务体系,实现工业技术、经验、知识的模型化、标准化、软件化、复用化。基于目前全球化的工业物联网发展态势,可以认为物联网在设备状态监测诊断中的应用范围、应用规模、应用成果将会不断扩大,应用效果也将向更好更优的水平发展。基于物联网的设备监测诊断系统架构如图4所示。
图4 基于物联网的设备监测诊断系统架构图
Fig.4 Architecture of monitoring and diagnosis system based on IoT
从整体的网络架构来看,设备健康监测物联网综合管理平台利用安装在设备上的传感器节点获取设备的健康状态监测信号和运行参数数据,经网络层集中上传至设备健康监测物联网综合管理平台,实现数据传输。应用层实现监测信号的分析、故障特征提取、故障诊断及预测功能,实现智能化管理、应用和服务。设备健康监测物联网综合管理平台具有强大的数据采集分析处理、数据可视、设备运维、故障诊断、故障报警等功能。通过实时监测查看、统计、追溯,实现对其管辖设备的实时监测和运行维护,基于运行信息和检修信息、自动生成设备管理报表,实现设备可靠性、故障数据、更换备件等信息统计,为维修方案制定提供依据。
针对不同需求,物联网综合管理平台可采用私有云方式建设,以独享宿主机资源方式,满足用户的资源独享、安全、合规需求;可通过HTTP、OPC等方式,实现与企业生产管理系统或第三方管理系统进行数据对接,打通数据关联通道。此外,除了物联网综合管理平台,物联网在设备状态监测诊断中的应用还包括通过设备状态监测诊断APP,以实现对设备运行数据的实时显示,及时了解设备突发故障,立即派发对设备维修任务,快速反馈对维修结果等。设备状态监测诊断、现场点检、DCS控制系统以及生产现场视频的整体融合,全面覆盖设备运行状态的整个监测过程。通过手机及内部办公电脑实现数据的及时查看、分析等,远程诊断中心与生产现场协同工作,实现诊断及现场验证的同步机制。
05 结束语
针对预测性维护价值数百亿元的新兴市场,本文提出以设备故障监测、诊断、预防性维护为手段,将物联网技术应用于设备状态监测诊断的思路,实现状态在线监测、远程故障诊断。智能制造升级需要匹配预测性维护能力的同步提升。因此,针对智能制造时代的生产需要,建议将普遍采用的计划性检修向基于设备健康状态的预测性维护转变。预测性维护的最终目标是提高生产安全稳定性、有效制定并实施设备维护策略、降低设备维护成本、减少设备停工检修时间。